The disruption and economic hardship caused by the ongoing pandemic have increased the urgency to accelerate smart manufacturing initiatives for future competitiveness. Manufacturers are using technology to stay connected, creating a new vision for how data is aggregated, shared, and acted upon to unite factories and people. Using automation, any organization can perform processes with little or no human intervention - creating a path to fulfill a variety of objectives in a wide array of manufacturing environments.
For decades, the personal computer (PC) and “industrial” variations have been used almost everywhere in the factory and plant environment. With all the failure-prone components, (like fans and hard drives) plus all the time it takes to keep the operating system up-to-date, the PC-centric period is coming to a close.
The movement to replace traditional PC hardware with “thin client” products has begun. Thin client products are diskless and fanless, with no hard drives, no storage space, no programs to upload or update, and sometimes not even a resident operating system.
Tethered-hardware thin-clients and mobile equivalents—tablets, smartphones, and other portable devices, deliver vastly improved productivity and yield drastically reduced total cost of ownership.
This use of WiFi-connected tablets, smartphones, and mobile devices is starting to generate explosive growth in industrial automation and process control. Integration of mobile technology is changing the landscape rapidly. Investing in mobile solutions purposely built for the needs of manufacturers today, can improve efficiency and optimize resources to remain competitive and meet key business goals. In addition, changing from a paper process to inputs and displays on mobile devices:
- Simplifies inventory management and strengthens quality control - According to a survey of manufacturers, more than 90% believe that product quality defines their success in the eyes of their customers. (Machine Design, 2019)
- Dramatically boosts worker productivity - Hard-mounted devices do not allow workers and managers the flexibility to take along and access critical information wherever they are in the plant, which is essential to real-time data sharing and fast decision making.
- Vastly reduces errors - Automation is so effective because it increases quality, output, and efficiency by reducing human assistance, thereby dramatically slashing the risk of error.
- Speeds up the reporting process - manufacturers are focusing on predictive maintenance, which can identify potential issues before they become a reality. With the right mobile device in hand, workers can capture, share, and respond to maintenance data in a way that can dramatically impact the quality of the end product and the overall productivity of the organization.
- And improves customer support - In the manufacturing world, productivity is measured in seconds, so workers need the ability to analyze information in real-time and solve critical challenges at a moment’s notice.
While the benefits of automation far outweigh the risks, there are still some significant challenges. Securely deploying mobile devices is a major issue, especially as integration with business applications means more sensitive information is accessible if a device is lost or stolen.
Enterprise Mobility Management (EMM) gives organizations the ability to track smartphones and tablets, to identify users on the network, and to deploy applications from a secure foundation. With sophisticated malware becoming more common in industrial and control environments, EMM is an essential tool to ensure mobile devices can be used without putting the system at significant risk.
To make the transition from a clipboard culture to a mobile environment outfitted with the optimal device deployment, manufacturers should find a trusted partner that understands their business needs and can provide devices configured for their work. We can help frame this and implement solutions to support your automation goals.
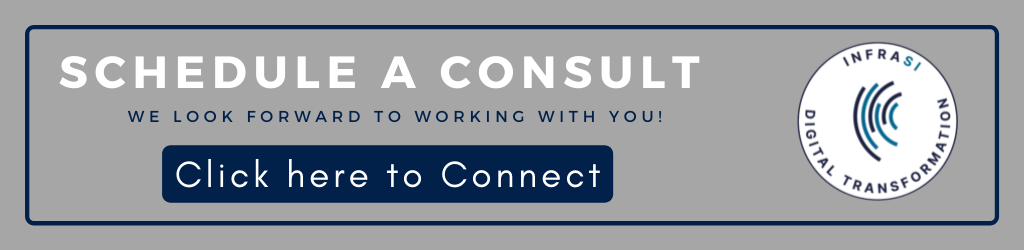